The Diorama is made of 2 modules - the first one contains a T34 85 wreck and measures 60 x 60 centimeters.
At first some pictures of the finished module.












Building report of the 1st Module of the diorama "suspicious noises in front of the T34"
Scale 1:16
The context of the Dios:
Hungary in the late summer of 1944. German soldiers have temporarily taken a destroyed factory. A Russian T 34 85 is burned in a bombed-out factory workshop.A German soldier noticed on the opposite side of the hall a suspicious movement and immediately stop in the MP40. An SS Untersturmführer looked over at him enquiring, his cigarette still in hand.
Kits of the 1st module:


The T34 as I receive it. The modell is by Wasan, buyed privat in ebay.
Not yet completely built, the battery defect, mechanics?, battery box grotty installed .... but anyway .... because of this it should be a wreck on a diorama.

The T34:
The damage of the T34 was prepared.
The idler wheel and the first on the left have been removed (simulation of a hit), the track was cut and removed the rubber tires of the wheels (fire damage). The arm of the 2nd track roller was unhooked from the spring strut to represent a fraction of the shock absorber.
The left fender was removed and the armored hull over the hit point was damaged.
The T34 will stand on a heap of rubble.






The opening of the ventilating fan has been cutting-off with the Dremel.
A few details of the armored hull were added and the damaged area was sanded. The front-left suspension arm has got a flange for the blasted wheel. This will be completed by bolt holes or broken screws.
The rear independent arm on the right side were hung from the struts, otherwise the wheels will not touch the ground, because the vehicle is hanging due to the lack of wheels on the left side front.




Meanwhile, the external tanks are assembled and dented. For this they were heated over a candle and carefully with the back of a knife pressed the dents. It must be very careful in order not to let it look unrealistic.
The procedure was the same way with fenders.
The blades of ventilation opening below the cut-out protection grids were simulated with cardboard.



I then subjected the whole tank a fading, ie: with a toothpick, I distributed over the entire surface little color points with oil paint burnt umber,English Red bright, white and green earth. These were spread with a brush in the direction of flow, and then further processed by dilution.
The fan blades were painted burnt umber and english red light.


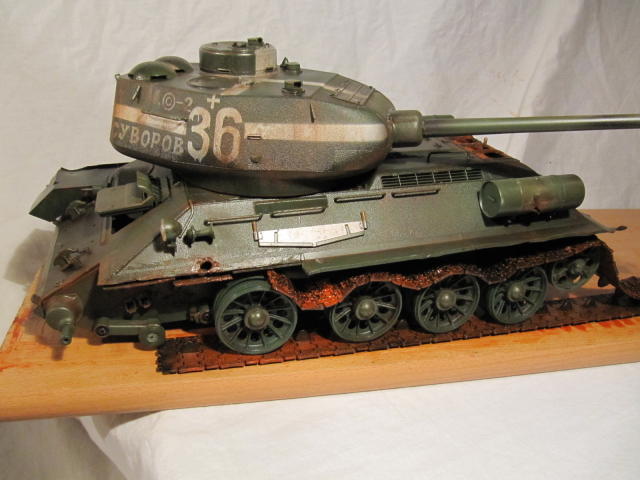

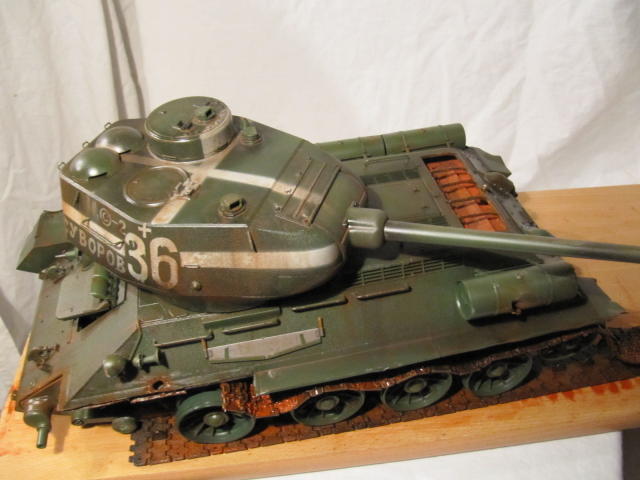
Finally, I have treated the tracks with highly diluted oil colours english red bright.
Further processing takes place after the drying of oil paint.
Now, the detailing of the T34 at the site of damage has been again revised.
The headlamp lens was destroyed,the disrupted cable to the headlamp and horn was made of florist wire.
The idler wheel has now been completed yet, but damaged. The chain was again separated and placed over the idler pulley.
The shot down wheel was treated . 5 holes were added to the flange of the wheel . Short pieces of florist wire were glued into the holes to simulate broken screws. Finally everything was again treated with oil paint english red light. The wet paint was sprinkled with pastel chalk orange and gently dabbed them lightly with a brush.



Now a further treatment was done with oil paints, pastels and pigments.
First, the armoured hull on the damaged side was painted with thinned oil paint English Red Light.Then came a careful washing with dilution.
Onto the wet paint I scraped chalk pastel orange with a knife.
With a stiff brush I dabbed and smeared wheels, radial arm and the side wall of the armoured hull) until the desired effect was achieved by me.
The rest of the armoured hull and the turret, I treated with Europe Dust pigment (Mig pigments)
Since the color of the oil washings wasn't dry, the pigments adhered pretty neat.
The chassis and the wheels I smeared with pigment fixer and dabbed with pigments Europe Dust.
Beware!! Never smear the pigments, because the pigment will immediately dissolve and become brown color without the desired dust effect!
At locations with a higher degree of pollution take enough pigments with the brush and dab at the wet spot.
Make sure the consistency is not too wet!
After the damaged side was also treated with Dust Europe in order to create a correct transition between the intact and the damaged side.
Finally, the chain was also treated.
Dust to Europe was in the structures of the chain rubbing.
This works very well, since the oil paint is not quite dry.
At locations with higher degree of pollution apply enough pigments with the brush and dab at the wet spot.







If everything is completely dry, the whole thing is sealed with matte clear coat carefully.
This is followed by further processing.
I've done a few things.
The damaged wheel was treated - englishrot, pastel orange, and even more Europe Dust.
The replacement tracks were attached to the bow and treated. The tow ropes are still treated and fixed.
So once again:





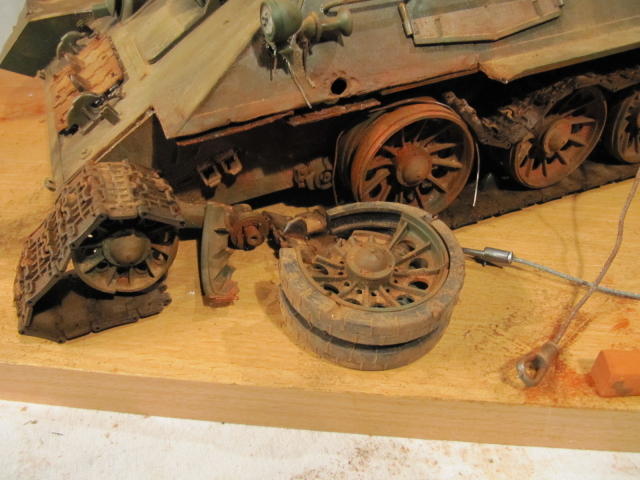



The burn marks were needed.
First, the T34 in places on the "burnt" side brushed with water and then sprinkled salt on it.
Once this had dried, I sprayed with the airbrush a bit of white about it.
After a short time I solved with a not too wet bristle brush by lightly brush over the salt.
It was a mottled appearance, which looks very realistic.
The images of the creation:




Now the whole thing on the same principle has been colored in black to simulate grime.
The first picture with salt, then processed the images, ie: salt is removed and treated with black pastel.















This was the building of the wreck.
I'll continue the report within a short time.
I beg your pardon for my bad english.
I hope, I haven't disgraced myself.
Best regards
Frank